- Overview
- Product Description
- Product Parameters
- Detailed Photos
- FAQ
Basic Info.
Model NO.
ZPDT420-35D
Tablet Shape
Oval, Rectangular, Round, Square
Warranty
Online Guidance
Maximum Tablet Pressure
120 kN
Maximum Tablet Production
170000 PCS/H
Number of Dies
35 Pairs
Net Weight
1420 Kg
Maximum Filling Depth (mm)Form
15
Precision
High Precision
Voltage
380V
Power(Kw)
5.5
Customized
Customized
External Dimensions(mm)
870*970*1560
Type
Tablet Press
Diameter of Upper and Lower Punch Rods(M
26
Maximum Pressure (kN)
20
Maximum Tablet Thickness (mm)
7
Maximum Diameter (mm)
16
Transport Package
Wooden Case Packaging
Specification
870*970*1420 mm
Trademark
Luning machinery
Origin
China
HS Code
8474801000
Production Capacity
170000 PCS/H
Packaging & Delivery
Package Size
107.00cm * 117.00cm * 176.00cm
Package Gross Weight
1620.000kg
Product Description
The rotary tablet press is a device that compresses various granular raw materials into round and irregular pieces. The speed of the turntable, the filling depth of the material, and the thickness of the tablet can be adjusted during compression.
1. The machine is compliance with the GMP requirement on the production of pharmaceuticals.
2. The compression parts is entirely separated from the driving mechanism.
3. The compression area is enclosed with transparent organic glass. To prevent contaminates. The compression area can be specially treated. All surface being smooth and easy to clean.
4. The mechanical buffer unit will prevent punches and apparatus from overload damage.
Stable Operation | Simple Operation | Widely Used
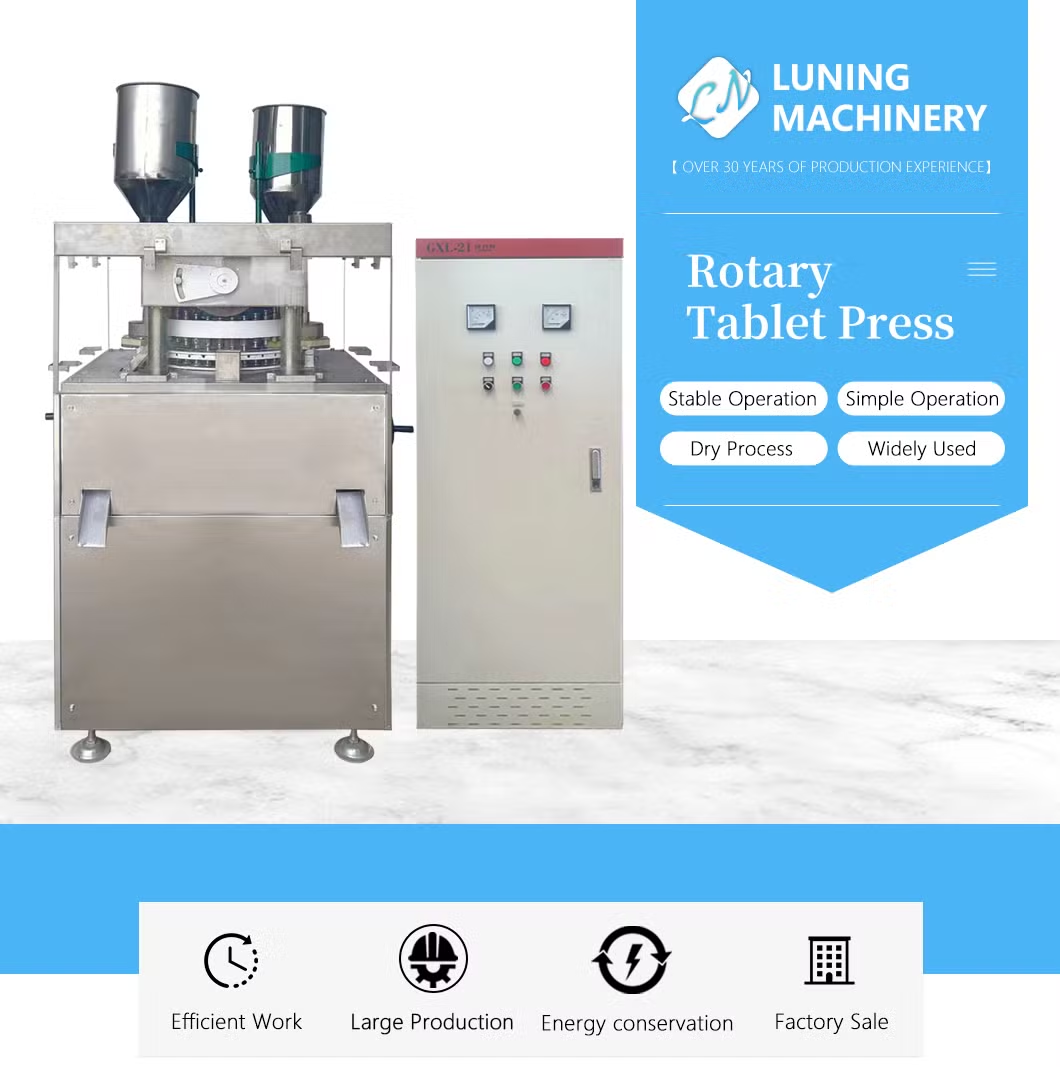
Working Principle of Rotary Tablet Press:
1. Feeding: Feed the powdered material to be compressed into the hopper of the rotary tablet press. The material can be a single raw material powder or a mixture of multiple components.
2. Filling: As the rotary tablet press rotates, the material enters the pressing chamber through a series of funnels or hoppers. In the compression chamber, the material is evenly filled into the grooves of the mold.
3. Pressing: After the material is filled into the mold, the pressing wheel (or punch) applies pressure to the material. This pressure compresses the material into sheets with a certain thickness and hardness.
4. Demolding: After the compression is completed, the tablets in the mold are pushed out of the mold through mechanical devices or air pressure and fall into the collector.
5. Discharge: Finally, the compressed tablets are discharged from the machine for subsequent processing such as drying, coating, etc.
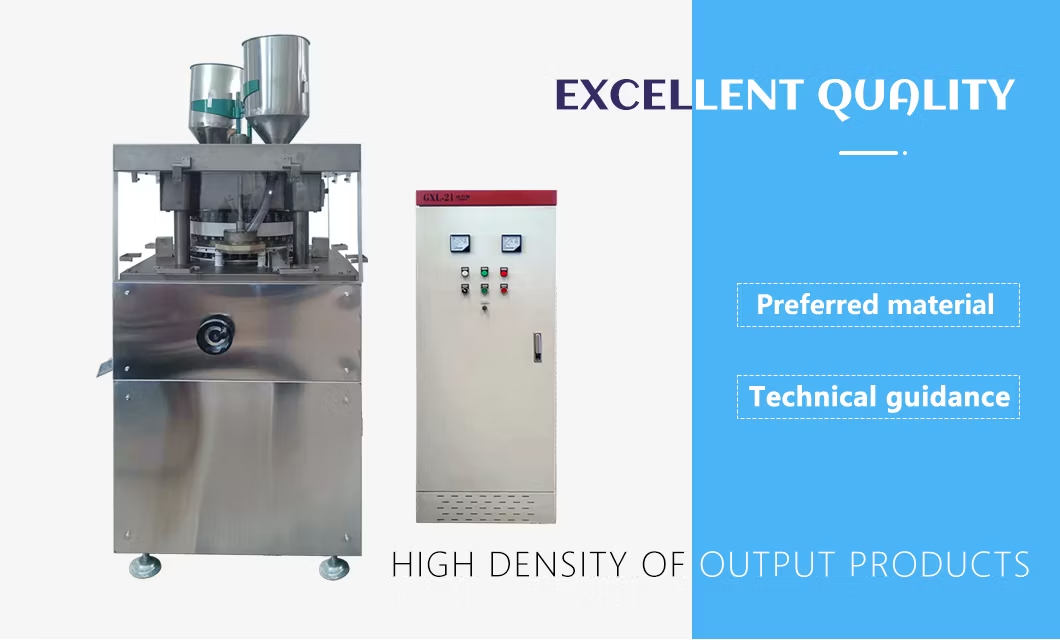

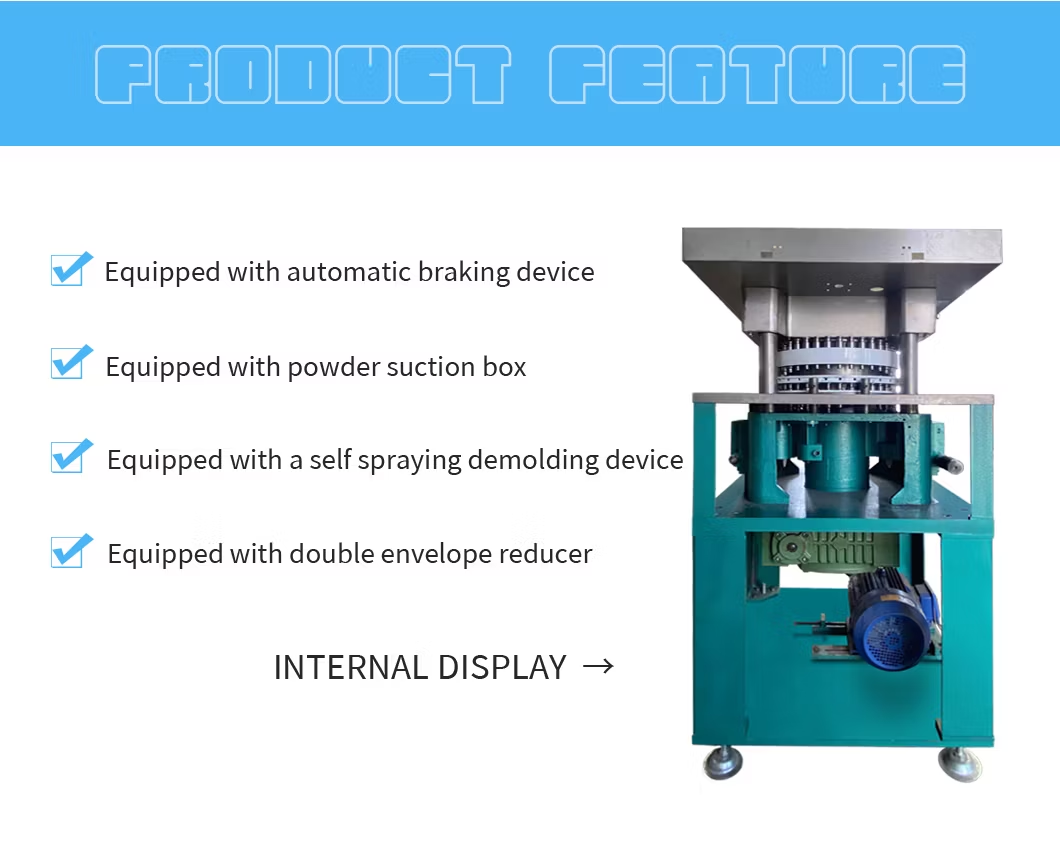
Product Feature
· Equipped with automatic braking device.
· Equipped with powder suction box.
· Equipped with a self spraying demolding device.
· Equipped with double envelope reducer.
The Rotary Tablet Press Has The Following Characteristics:
1. Efficient production: The rotary tablet press can continuously complete multiple steps such as filling, pre pressing, main pressing, and dispensing, significantly improving production efficiency.
2. Uniform pressure: Simultaneously applying pressure during upward and downward flushing ensures that the tablet receives even pressure, avoiding the phenomenon of top cracking caused by upward flushing and pressure.
3. uffer device: Equipped with mechanical buffer device and clutch device, it can protect the equipment from damage in case of machine overload or abnormal situation.
4. Automatic adjustment: The tablet pressing speed, material filling depth, and tablet pressing thickness can be adjusted to meet the production needs of different types and specifications of tablets.
5. Powder suction device: The built-in powder suction box can effectively absorb and filter the dust generated during the production process, keep the equipment clean, and prevent blockage.
6. Easy to operate, one-time molding, easy to clean and maintain. Low energy consumption, energy-saving and environmentally friendly, with a wide range of applications.
Easy To Operate And Easy To Us
· Reasonable design, can improve production efficiency, high output, low energy consumption, saving time and labor.
· Compared with the same type of tablet press, the pressure is higher and the strength is greater.
· Forced feeding system to make material filling more uniform.
· Further reduce maintenance rates and increase production efficiency.
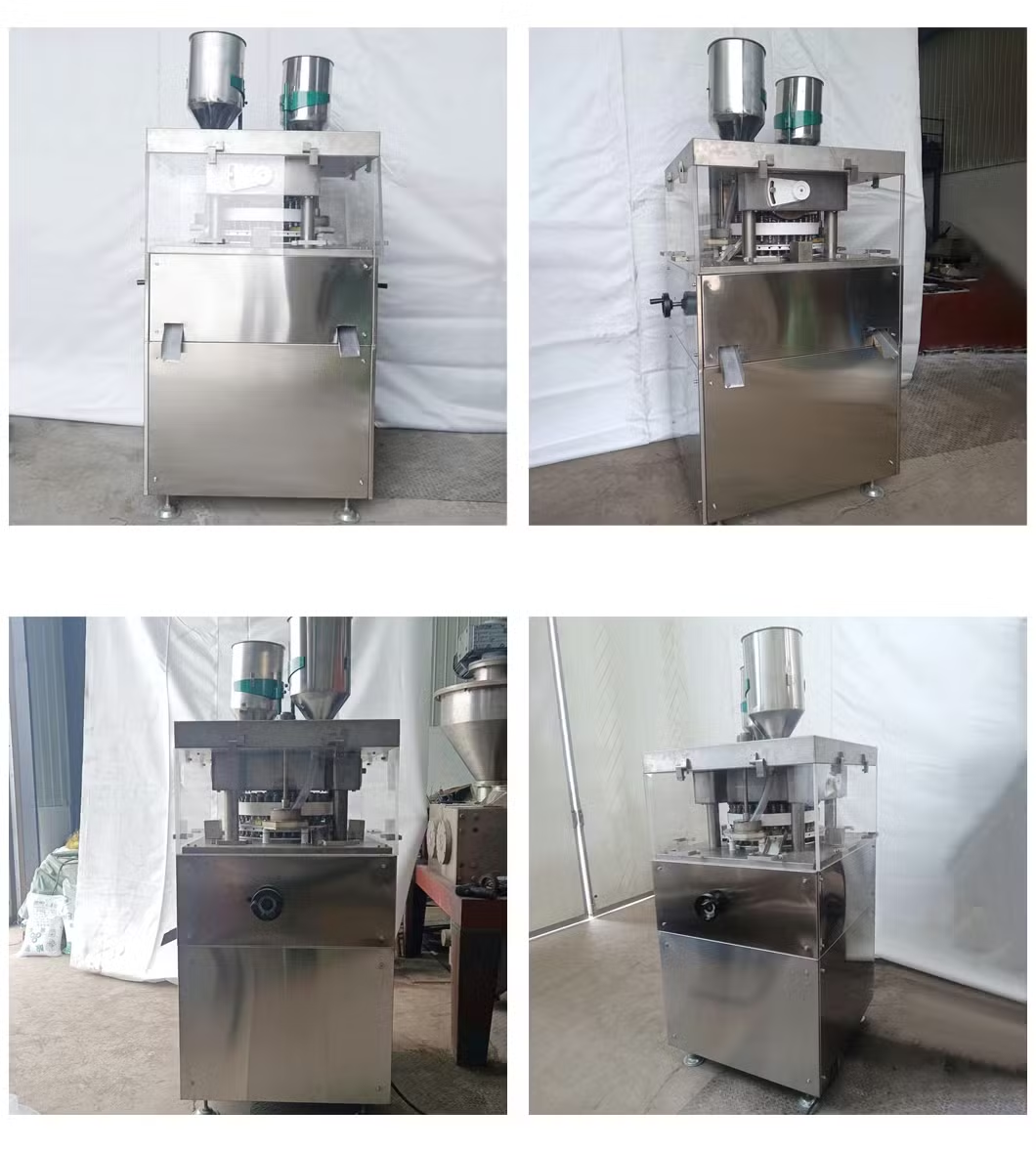
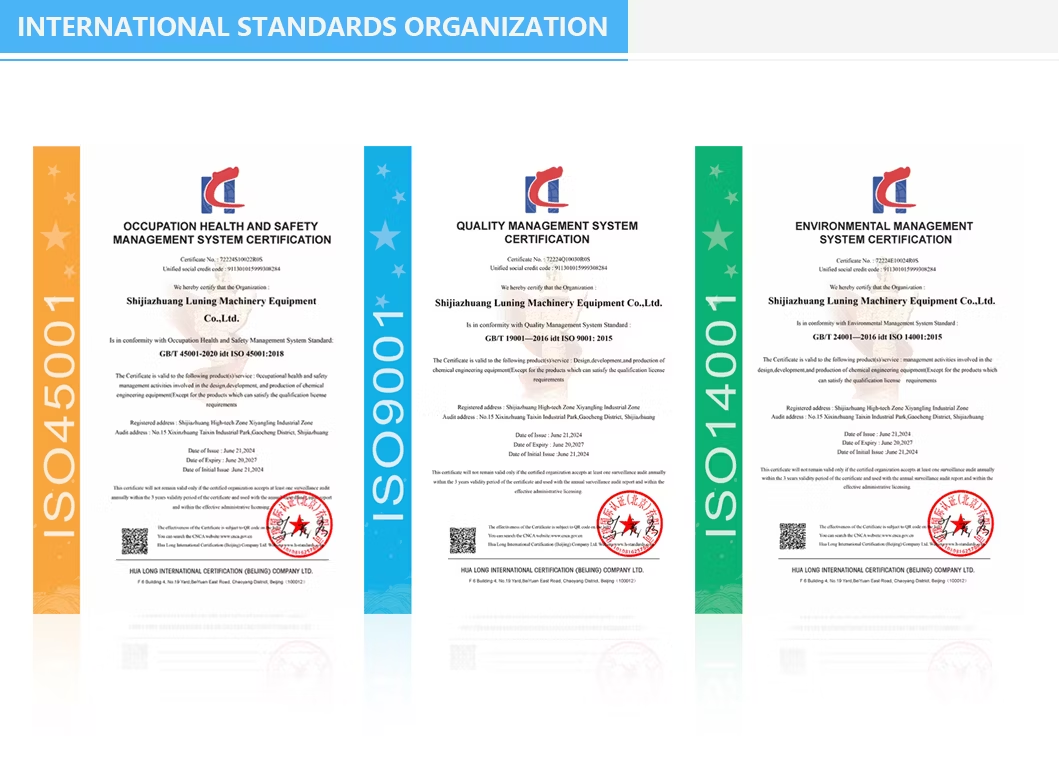

Q: Why should you choose our tablet press and packing machine?
A: We are specialists in tablet press and packing machines. Our products have gained global trust, being exported to Asia, the USA, the EU, and the Middle East.
Q: Will the machine be damaged during transport?
A: Rest assured, our goods come with standard export packaging to ensure safe transport.
Q: Do you offer after-sale services?
A: Absolutely. We have engineers on standby to provide overseas services.
Q: What are our advantages?
A: 1. Competitive pricing
2. Exceptional technical support
3. Unparalleled customer service
4. Superior quality machinery
Mold | ZPDT420-35D |
Number of Dies (Pairs) | 35 |
Maximum Pressure (KN) | 120 |
Maximum Diameter (mm) | 16 |
Maximum Tablet Thickness (mm) | 7 |
Maximum Filling Depth (mm) | 15 |
Maximum Rotary Speed (rpm) | 35 |
Diameter of upper and lower punch rods(mm) | 26 |
Outer diameter of the middle mold(mm) | 30 |
Maximum tablet production(pcs/h) | 170000 |
Power(KW) | 5.5 |
Net weight(KG) | 1420 |
Overall Dimensions (mm) | 870*970*1560 |
Machine footprint (mm²) | 1002*970 |
Stable Operation | Simple Operation | Widely Used
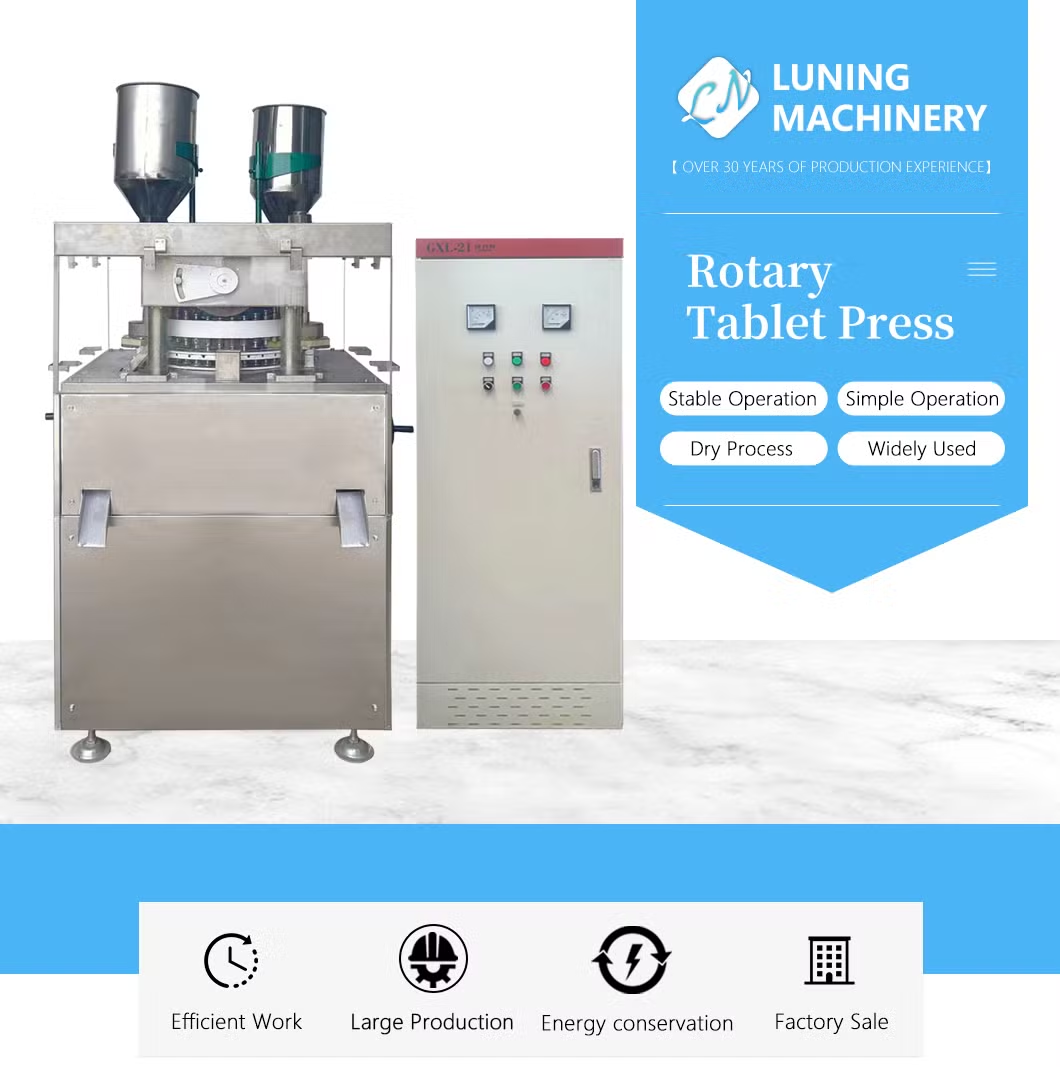

1. Feeding: Feed the powdered material to be compressed into the hopper of the rotary tablet press. The material can be a single raw material powder or a mixture of multiple components.
2. Filling: As the rotary tablet press rotates, the material enters the pressing chamber through a series of funnels or hoppers. In the compression chamber, the material is evenly filled into the grooves of the mold.
3. Pressing: After the material is filled into the mold, the pressing wheel (or punch) applies pressure to the material. This pressure compresses the material into sheets with a certain thickness and hardness.
4. Demolding: After the compression is completed, the tablets in the mold are pushed out of the mold through mechanical devices or air pressure and fall into the collector.
5. Discharge: Finally, the compressed tablets are discharged from the machine for subsequent processing such as drying, coating, etc.
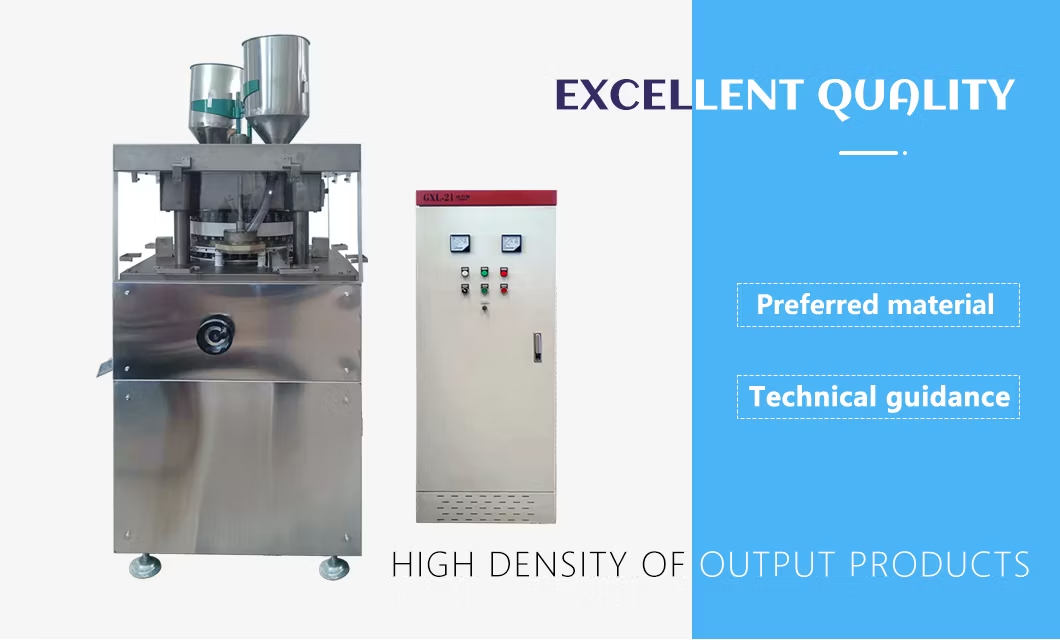

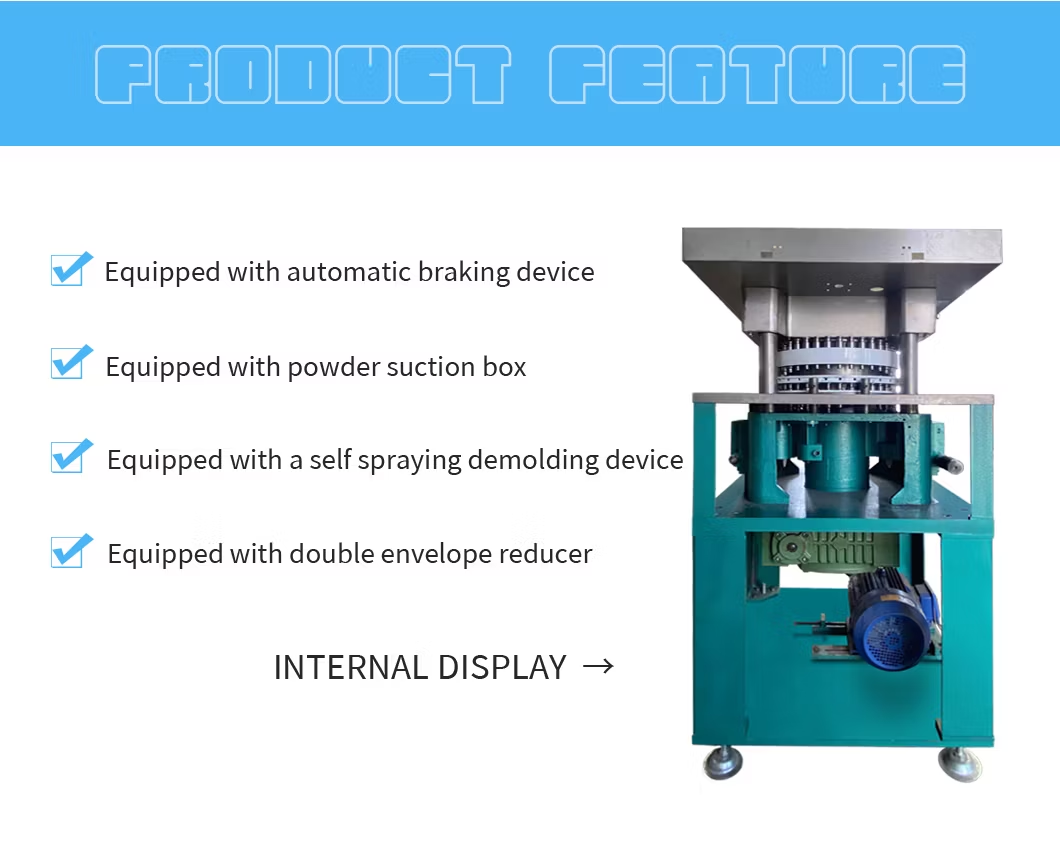
Product Feature
· Equipped with automatic braking device.
· Equipped with powder suction box.
· Equipped with a self spraying demolding device.
· Equipped with double envelope reducer.

1. Efficient production: The rotary tablet press can continuously complete multiple steps such as filling, pre pressing, main pressing, and dispensing, significantly improving production efficiency.
2. Uniform pressure: Simultaneously applying pressure during upward and downward flushing ensures that the tablet receives even pressure, avoiding the phenomenon of top cracking caused by upward flushing and pressure.
3. uffer device: Equipped with mechanical buffer device and clutch device, it can protect the equipment from damage in case of machine overload or abnormal situation.
4. Automatic adjustment: The tablet pressing speed, material filling depth, and tablet pressing thickness can be adjusted to meet the production needs of different types and specifications of tablets.
5. Powder suction device: The built-in powder suction box can effectively absorb and filter the dust generated during the production process, keep the equipment clean, and prevent blockage.
6. Easy to operate, one-time molding, easy to clean and maintain. Low energy consumption, energy-saving and environmentally friendly, with a wide range of applications.

Easy To Operate And Easy To Us
· Reasonable design, can improve production efficiency, high output, low energy consumption, saving time and labor.
· Good tablet press equipment can produce qualified flake products.
One-time Molding
· Mechanical pressure forced compression molding, without adding any wetting agent.details reflect quality
Details Reflect Quality 
· Mechanical pressure forced compression molding, without adding any wetting agent.details reflect quality

· Compared with the same type of tablet press, the pressure is higher and the strength is greater.
· Forced feeding system to make material filling more uniform.
· Further reduce maintenance rates and increase production efficiency.
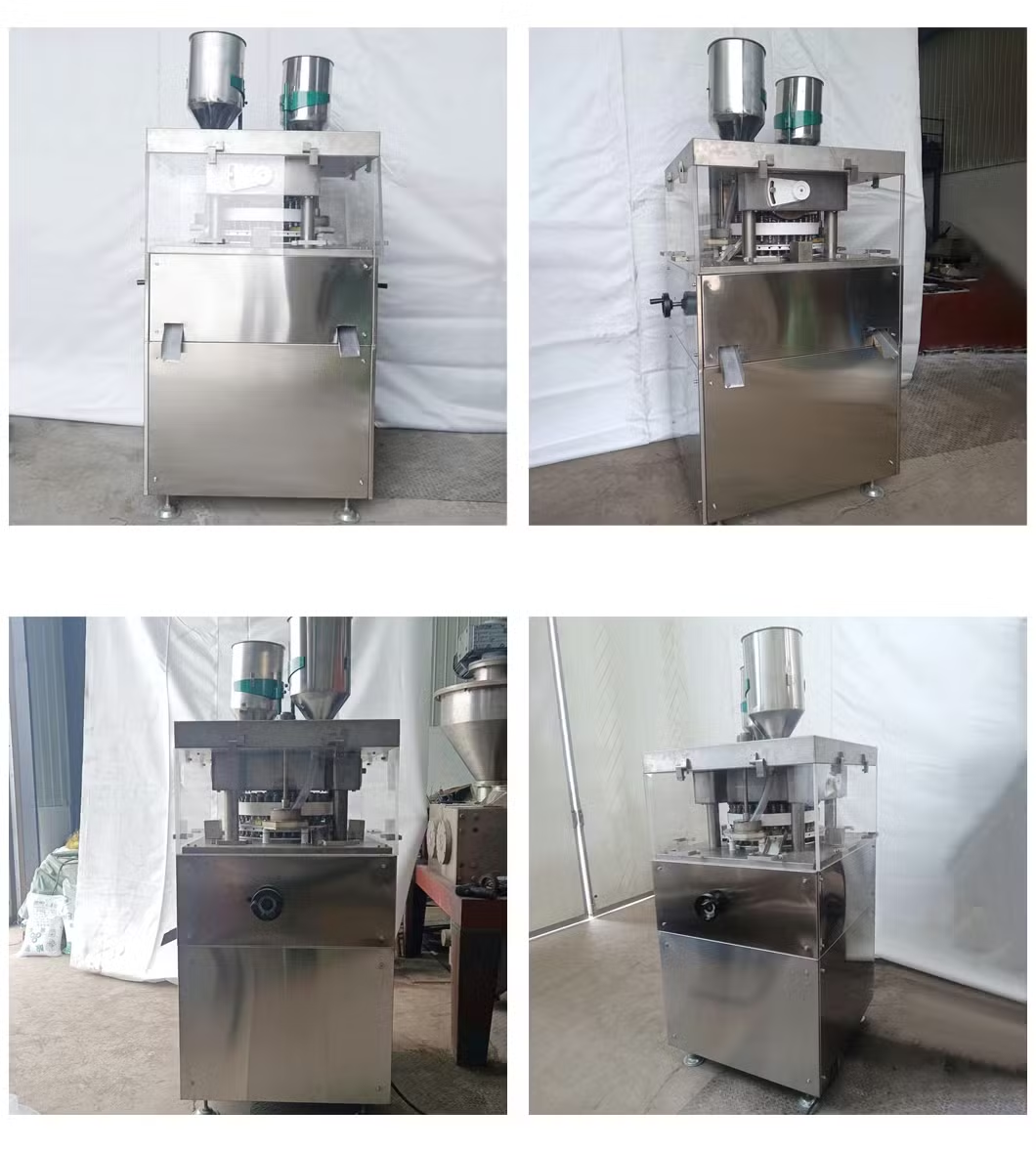
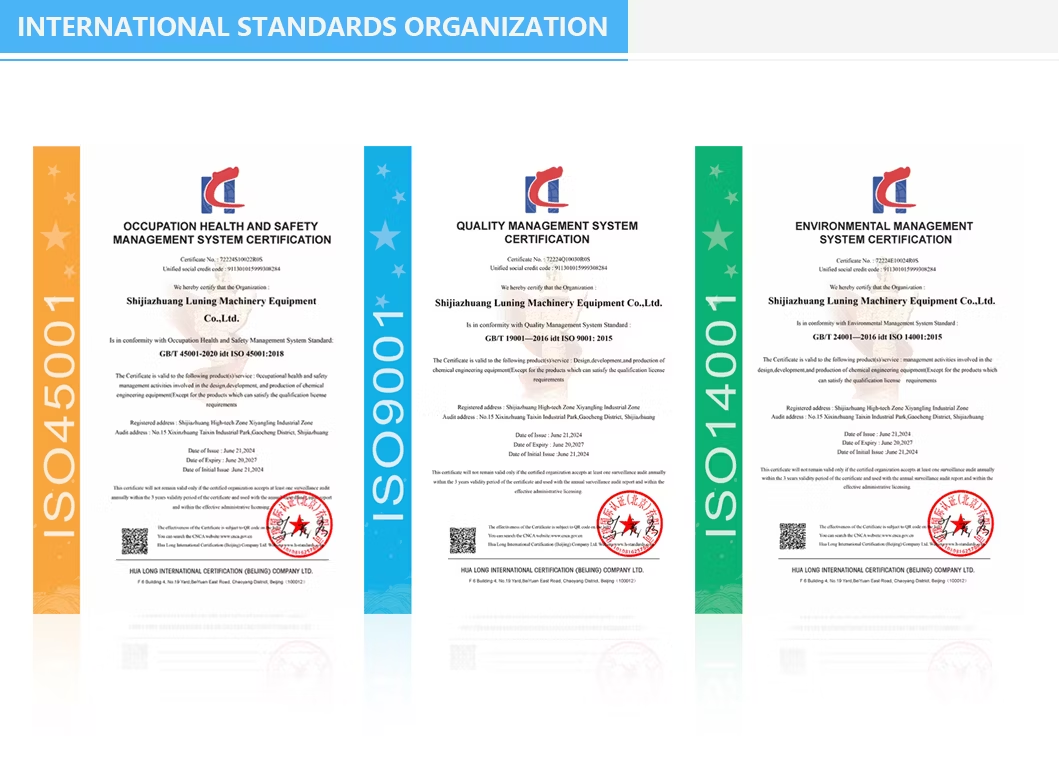


Q: How to choose the suitable one?
A: Kindly provide your detailed requirements via email or online. We will then recommend the most suitable machine tailored to your needs.
As per your request.
Q: What payment methods do you prefer?
Q: Why should you choose our tablet press and packing machine?
A: We are specialists in tablet press and packing machines. Our products have gained global trust, being exported to Asia, the USA, the EU, and the Middle East.
Q: Will the machine be damaged during transport?
A: Rest assured, our goods come with standard export packaging to ensure safe transport.
Q: Do you offer after-sale services?
A: Absolutely. We have engineers on standby to provide overseas services.
Q: What are our advantages?
A: 1. Competitive pricing
2. Exceptional technical support
3. Unparalleled customer service
4. Superior quality machinery